SPEAKER
BRIEF
Design a portable bluetooth speaker based on existing electronics. The design must:
Be manufactured from injection moulded plastic.
Incorporate electronics circuitry and components from an existing bluetooth speaker.
DESIGN SOLUTION
A portable bluetooth speaker designed to be easily operated for young apartment dwellers. The speaker was designed for cost effective manufacture and assembly. The design houses electronics from an existing speaker.
TOOLS & SOFTWARE
Autodesk Fusion 360
Analogue Sketches
Adobe Photoshop
PowerPoint
FABRICATION TECHNIQUES
3D printing
Laser cutting
Basic electronics
Priming, painting and finishing
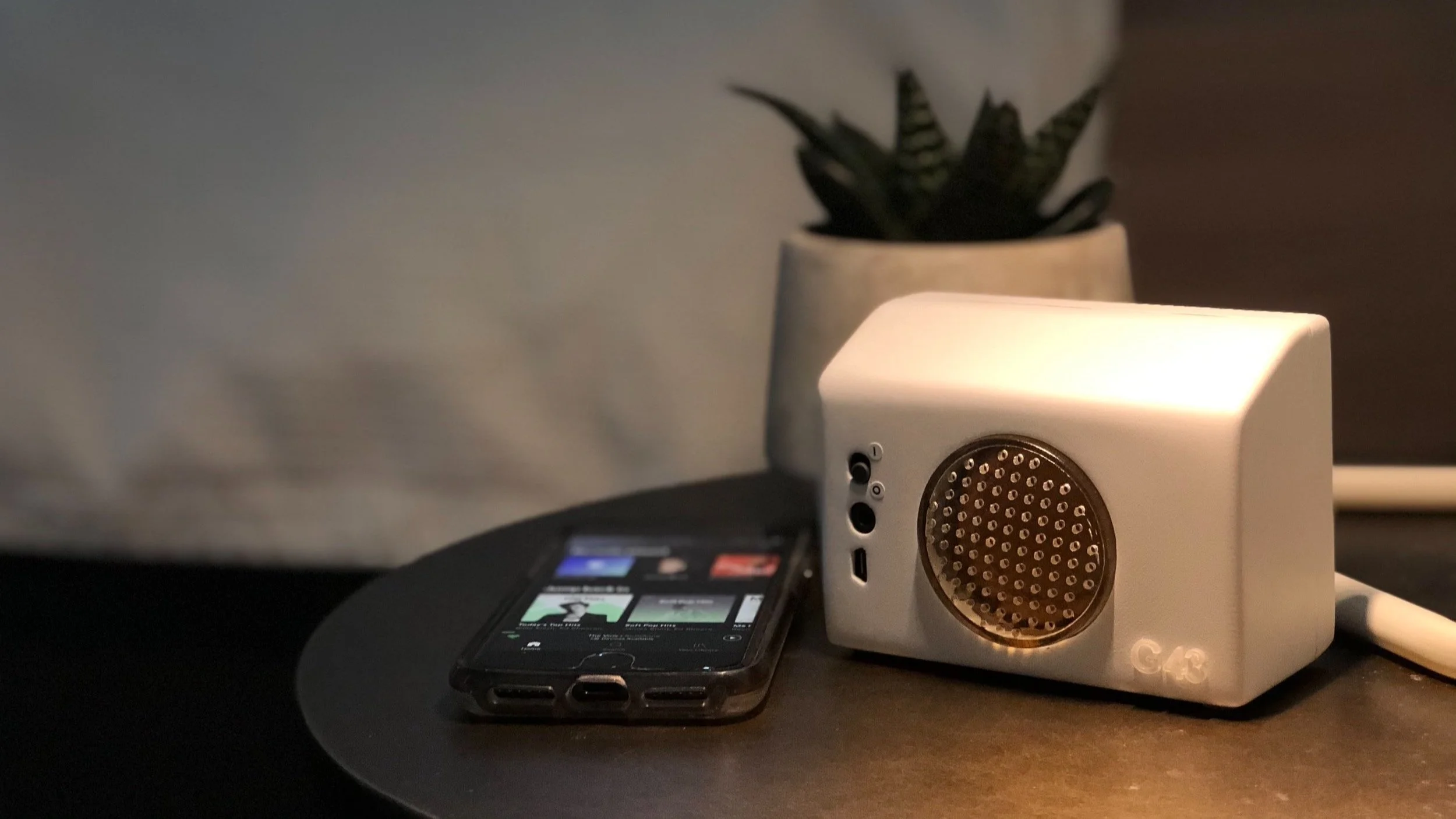
BACKGROUND
The purpose of this project was to get a deep understanding on injection moulding to design a portable speaker for cost effective manufacture and assembly using electronics from an existing speakers.
RESEARCH
This project involved secondary research, including injection moulding design guides research, materials research and market research.
PROBLEMS & OPPORTUNITIES
Few opportunities were identified on the research. These include reduced number of parts, affordable materials appropriate for injection moulding and implementation of features (ribs) to position parts.
DESIGN SOLUTION
A portable speaker designed for cost effective manufacture and assembly. This is achieved through low number of parts, adequate draft, consistent wall thickness and round edges.
DESIGN SOLUTION
PORTABALE SPEAKER
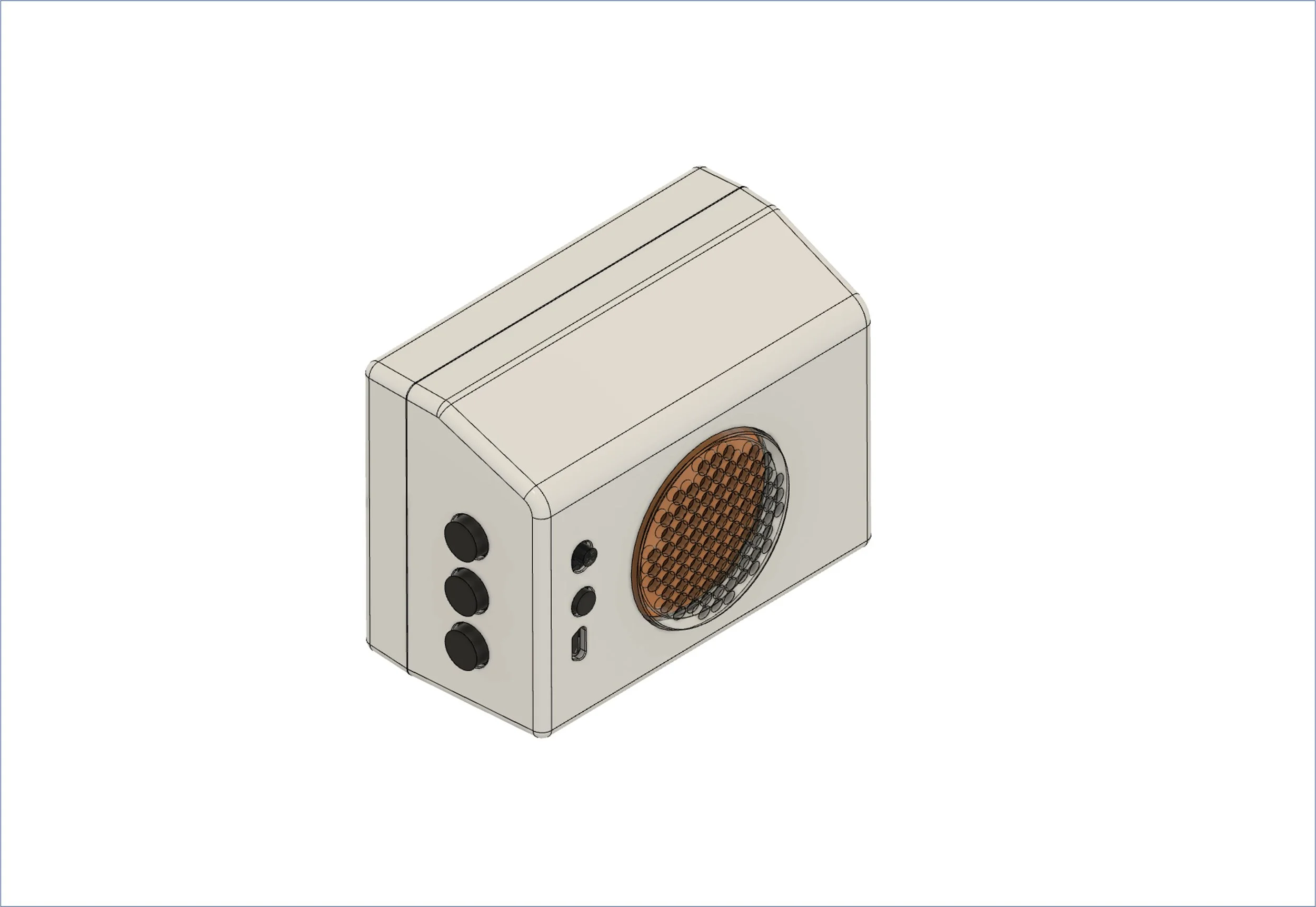
EXPLODED VIEW
EXPLODED VIEW AND BILL OF MATERIALS
INTERNAL PARTS
DESIGN PARTS & ELECTRONICS






MANUFACTURING DETAILS
MANUFACTURING PROCESS
The speaker was made using Injection Moulding Process as it is low cost and suitable for manufacturing small and medium size parts with complex shapes.
MATERIAL AND TEXTURES
The only material utilised for the design was Acrylonitrile Butadiene Styrene (ABS). Benefits include low cost, quality & durability (Lefteri, 2012; Thompson, 2017). Matte finish was applied on all plastic parts except grill. Gloss finish was chosen for the grill.
DRAFT ANALYSIS & WALL THICKNESS
Over 1 degree of draft angle was applied to all nominal walls, ribs and bosses. This assist with part ejection and texture requirements. Wall thickness was chosen in accordance with injection moulding design guides and the chosen material recommended range (ABS).

FINAL PROTOTYPE

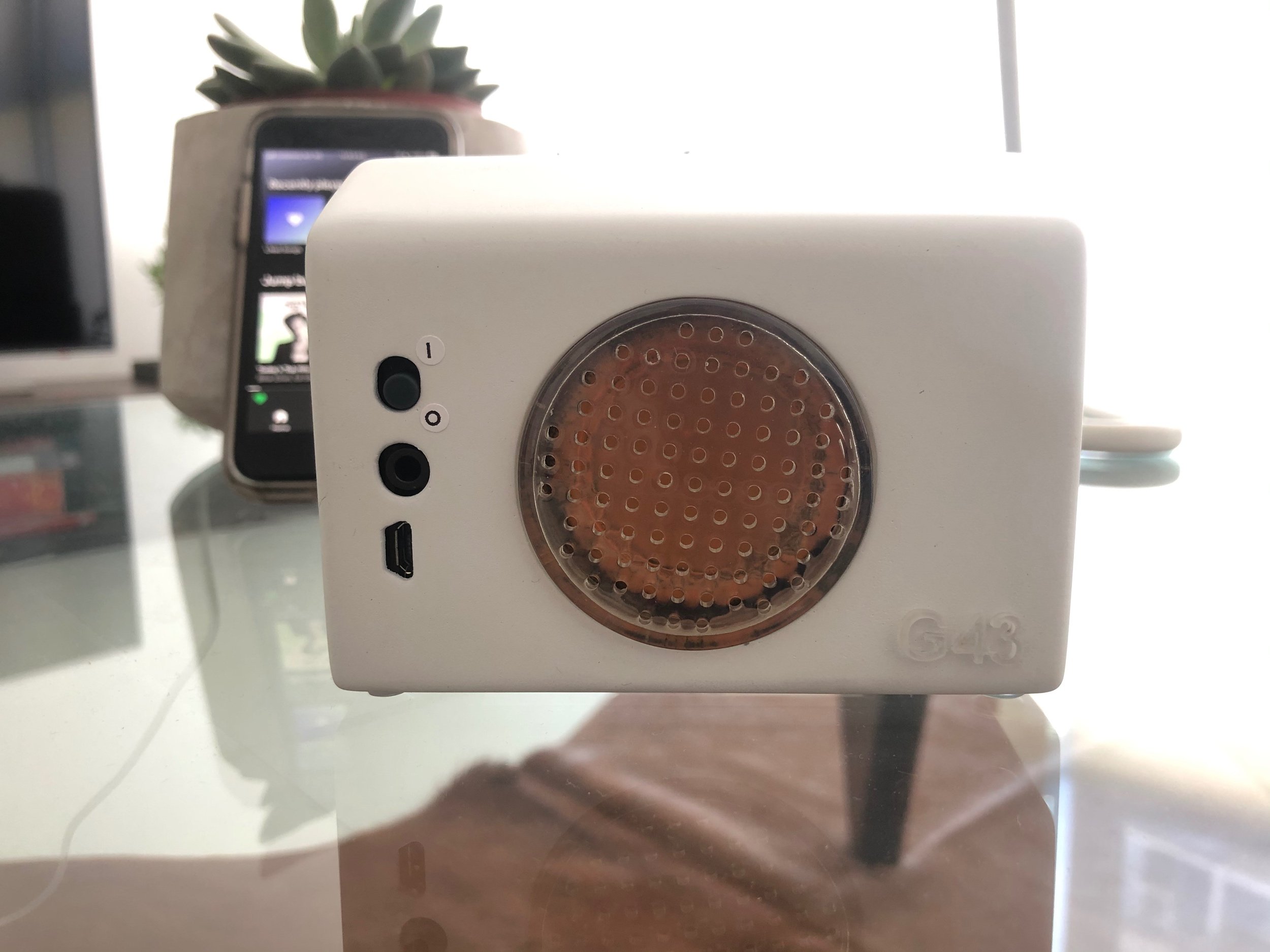



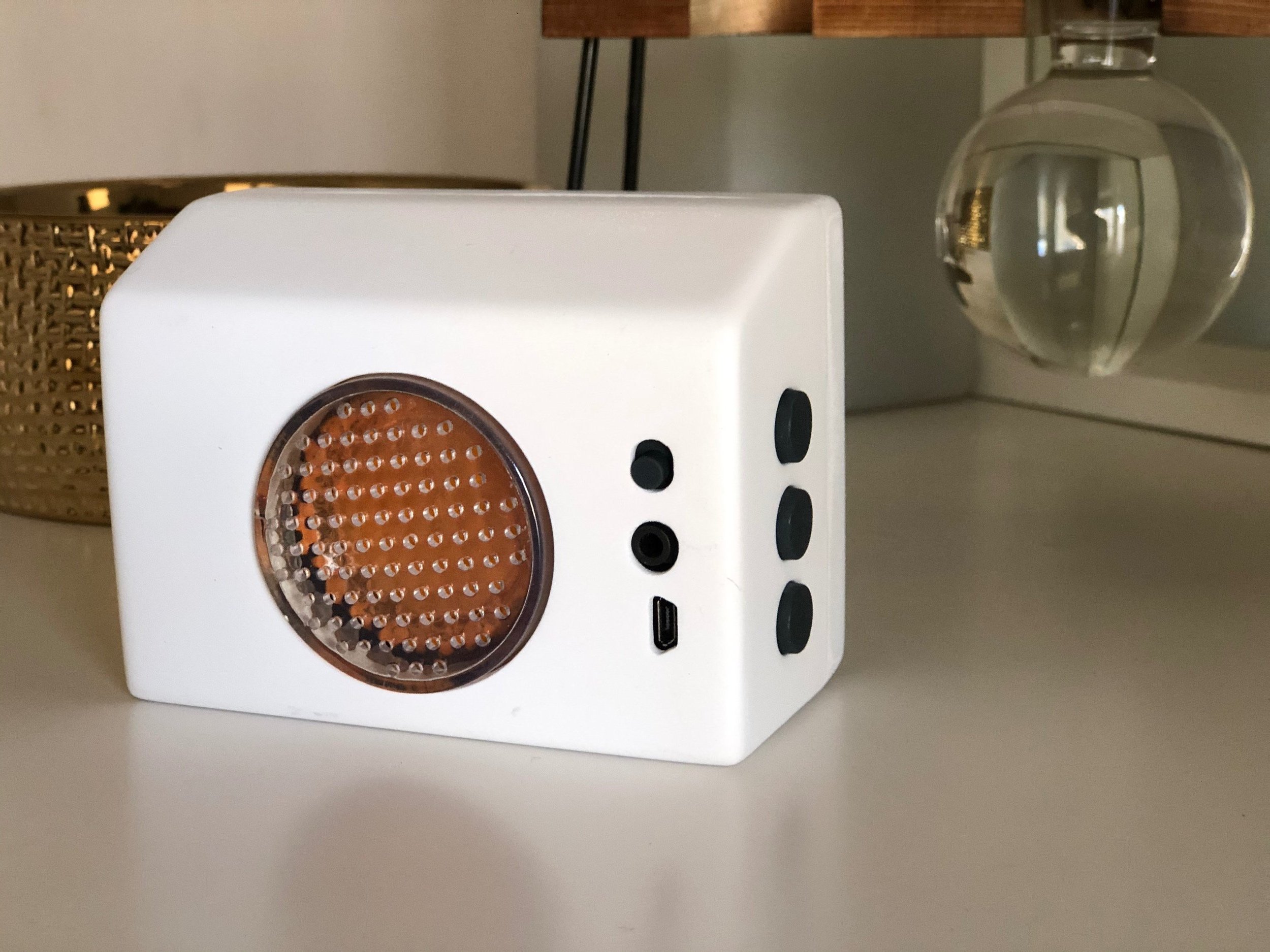
DESIGN PROCESS OVERVIEW
Manufacturing Process & Material Research
Market Research
Brainstorming
Ideation
Concept Development & Iteration
Prototyping
Concept Refinement
Final Functional Prototype